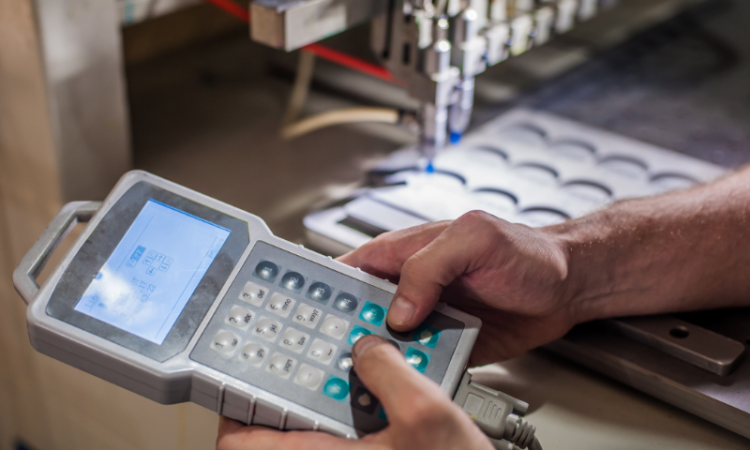
Liquid dispensing is a critical process in many industries, from pharmaceuticals to electronics. However, even the best precision dispensing systems can encounter issues that disrupt production. Understanding these common problems and applying quick fixes can save time, reduce waste, and maintain the quality of your output. Here are some practical solutions you can implement immediately to address the most frequent liquid dispensing challenges.
1. Addressing Inconsistent Flow Rates
Inconsistent flow rates are a prevalent issue in liquid dispensing processes. This problem can arise due to various factors such as clogged nozzles, incorrect fluid viscosity, or improper equipment calibration. To fix this, start by checking the nozzle for any blockages. A quick clean with the appropriate solvent can often resolve this issue. If the problem persists, verify that the fluid viscosity matches the requirements of your dispensing system. Adjusting the viscosity by either heating or cooling the liquid or adding a diluent can help achieve a smoother flow. Finally, recalibrate your liquid dispensing equipment to ensure that it is functioning at optimal settings. These steps should quickly restore consistency in flow rates.
2. Fixing Drips and Leaks
Drips and leaks are not just wasteful but can also lead to product defects, particularly in precision dispensing tasks. These issues typically result from worn-out seals, improper pressure settings, or faulty nozzles. The first step in addressing drips and leaks is to inspect the seals and gaskets in your liquid dispensing equipment. If they appear worn or damaged, replace them immediately to prevent further leakage. Next, check the pressure settings; excessive pressure can force liquid out of the system even when it is not dispensing. Adjust the pressure to the manufacturer’s recommended levels. Additionally, ensure that the nozzle is correctly attached and free from any damage. A secure and undamaged nozzle is essential for preventing leaks during the dispensing process.
3. Tackling Inaccurate Dispensing Volumes
Accuracy in dispensing volumes is crucial for maintaining product quality, especially in industries that rely on precision dispensing. If you notice that your system is dispensing incorrect volumes, the issue may lie in the calibration or the dispensing cycle settings. Begin by recalibrating the equipment according to the specifications of the liquid being dispensed. Calibration ensures that the system dispenses the correct amount of liquid with each cycle. If recalibration does not resolve the issue, review the dispensing cycle settings. The cycle time, pressure, and other parameters must be finely tuned to match the characteristics of the liquid. Making these adjustments should correct any inaccuracies in the dispensing volume.
4. Resolving Poor Adhesion or Coverage
Poor adhesion or inadequate coverage is another challenge that can arise in liquid dispensing, particularly when dealing with coatings or adhesives. This issue can stem from improper surface preparation, incorrect fluid viscosity, or inadequate pressure settings. To improve adhesion, ensure that the surface to be coated is clean and free of contaminants. A thorough cleaning with a suitable solvent can enhance surface readiness. Adjusting the viscosity of the liquid can also improve its ability to adhere to the surface. Thicker fluids may require heating to reduce viscosity, allowing for better flow and coverage. Finally, ensure that the pressure settings are appropriate for the application. Too much pressure can cause the liquid to spread too thinly, resulting in poor coverage.
5. Dealing with Clogged Nozzles
Clogged nozzles are a frequent issue in liquid dispensing systems, particularly when working with high-viscosity fluids or adhesives that tend to dry quickly. Regular maintenance and immediate cleaning are essential to prevent clogging. If a nozzle becomes clogged, disassemble it and clean it thoroughly using a solvent compatible with the liquid you are dispensing. Ensure that all residue is removed before reassembly. Additionally, implementing a routine cleaning schedule can help prevent clogs from occurring in the first place. For liquids that are prone to drying out, consider using a system with automatic nozzle cleaning features to maintain smooth operation.
Conclusion
These quick fixes for common liquid dispensing issues can significantly improve your production process, ensuring that your equipment operates at peak efficiency. Regular maintenance, proper calibration, and attention to detail can prevent these issues from recurring and keep your production line running smoothly.
For more information about liquid dispensing solutions, contact Unicontrols today.